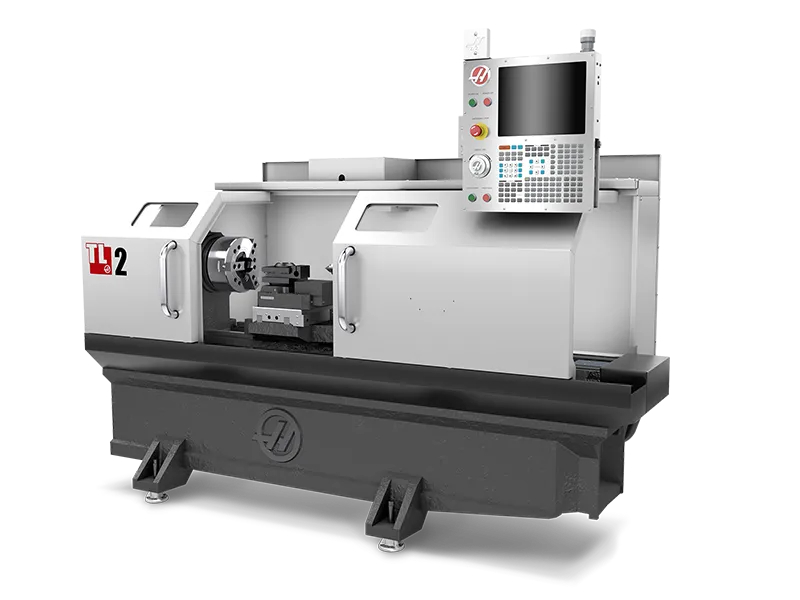
What is CNC?
Share
Introduction to CNC
You've probably heard people throw around the term CNC without really explaining what it means. CNC stands for computer numerical control, which sounds fancy but breaks down pretty simply.
Take any machine tool - a mill, lathe, whatever - and hook it up to a computer that tells it exactly what to do. That's your basic CNC setup right there.
Here's why CNC technology matters so much. Before these machines came along, making precision parts meant finding skilled machinists who could work by hand.
Good ones were expensive and hard to find. Even the best human operator makes small mistakes that add up over time. CNC machines don't get tired, don't have bad days, and don't accidentally move the wrong handle. You program them once, and they'll make the same part exactly the same way a thousand times.
The whole computer numerical control idea started back in the 1940s when aircraft manufacturers needed complex parts made consistently. Early CNC machines used punch cards and paper tape - pretty crude by today's standards. Modern CNC technology runs on regular computers with software that makes programming much easier than the old days.
Walk around your house and count how many things probably got made on CNC machines. Your kitchen appliances, car parts, electronic devices - most of them started as raw material that got shaped by CNC machining processes.
The precision you get from computer numerical control systems opened up possibilities that just weren't practical when everything had to be done by hand. Small shops can now make parts that used to require huge factories with armies of skilled workers.
Understanding CNC Machining
CNC machines work by following step-by-step instructions stored in a computer program.
The computer sends signals to motors that move cutting tools and workpieces to exact positions.
This process repeats identically for every part, removing the chance for human error that happens with manual operation.
CNC machining delivers consistent results because the machine follows the same programmed sequence each time.
Software plays a central role in CNC operations. Designers use CAD programs to create detailed part drawings on computers. CAM software takes these drawings and generates the actual machine instructions.
This programming stage determines which tools cut the material, how fast they spin, and the precise path they follow. Different CNC machines need specific programming methods, but computer numerical control principles apply across all types.
CNC technology handles operations that manual methods struggle to achieve. CNC mills cut intricate shapes from solid blocks of metal or plastic. CNC lathes spin parts while tools shape them into round components.
Plasma cutters slice through heavy steel plates with computer-guided precision. Advanced machines move in multiple directions simultaneously, creating complex geometries that would challenge even skilled manual operators.
The accuracy of CNC machining comes from computer numerical control removing human inconsistencies. A properly set up CNC machine makes part number 1000 identical to part number 1.
Modern machines hold tight tolerances across large components, maintaining precision that manual work cannot match reliably. This repeatability explains why CNC technology became standard in manufacturing - you get the same quality results every production run.
Types of CNC Machines
CNC mills are what most people picture when they think about computer numerical control.
These machines spin cutting tools while the workpiece stays put on a table. The computer moves everything around to cut shapes, drill holes, and make features that would take forever by hand.
You can get vertical CNC mills where the spindle points down, or horizontal ones that stick out sideways. Both types follow the same basic idea - the computer tells the machine where to go.
CNC lathes work differently because they spin the part instead of the tool. These machines are perfect for round stuff like shafts and bushings. The computer numerical control system keeps track of where the cutting tool goes while the part spins.
Many modern CNC lathes can do more than just turning - they drill holes and cut threads without moving your part to another machine.
Plasma cutters are the workhorses for cutting thick steel. These CNC machines use an electric arc that melts through metal like a hot knife through butter.
The computer follows a programmed path to cut whatever shape you need. Plasma cutters work way faster than sawing or grinding, and the edges come out clean enough to weld without extra work.
Then you have the specialty machines that handle jobs the basic types can't do. Laser cutters use light beams to slice thin materials with incredible detail.
Water jet cutters shoot high-pressure water to cut through anything without heating it up. Wire EDM machines use electricity to cut shapes in hardened steel that regular tools can't touch. Each CNC machine type does certain jobs better than others - pick the right one for your material and part requirements.
Applications of CNC Machining
Aerospace companies depend heavily on CNC applications because aircraft parts need precision that manual methods simply cannot deliver. Every engine component, wing bracket, and landing gear part gets made on CNC machines.
The computer numerical control systems create parts with tolerances measured in thousandths of an inch - mess up by even a little bit and planes don't fly safely. Titanium and aluminum parts that would take weeks to make by hand get finished in hours using CNC technology.
Medical device manufacturing represents another major area where CNC machining shines. Surgical instruments, implants, and diagnostic equipment all require precision that saves lives.
A hip replacement joint made on CNC machines fits perfectly because the computer numerical control system follows exact specifications. Small parts like screws for bone surgery need accuracy that human hands cannot achieve consistently. The biocompatible materials used in medical parts often require specialized cutting techniques that CNC technology handles automatically.
Automotive manufacturers probably use more CNC applications than any other industry. Engine blocks, transmission cases, and brake components all start as raw metal that gets shaped by computer numerical control processes. Modern cars contain hundreds of CNC machined parts - from tiny sensors to large structural components.
The volume requirements mean CNC machines run around the clock making identical parts for assembly lines.
Industrial CNC usage keeps expanding into new areas as the technology gets more accessible. Furniture makers use CNC machines to cut complex wood joinery.
Electronics companies rely on computer numerical control for precise circuit board mounting features. Even jewelry manufacturers adopted CNC technology to create intricate designs that hand carving could never match.
The common thread across all these CNC applications is the need for precision, repeatability, and consistency that only computer numerical control systems can provide reliably.
The Role of a CNC Machinist
Most CNC machinists learn their trade through a mix of classroom time and hands-on work. You don't need an engineering degree, but you better be comfortable with numbers and able to read blueprints.
Community colleges offer CNC training that covers the basics, but the real learning happens when you're standing next to a machine that costs more than most people's houses. Good machinists develop a feel for how different metals cut and which tools last longest.
A typical day starts with checking what parts need to get made and figuring out the best way to hold them in the machine. Sometimes the print looks simple but turns out tricky to clamp without the part moving.
CNC programming comes next - you write the code that tells the machine exactly where to move. Some shops have dedicated programmers, but most places expect their machinists to handle both programming and running the machines.
CNC programming separates the good machinists from the average ones. You need to know how fast you can push different materials before tools start breaking.
Computer numerical control systems do what you tell them, but they won't stop you from making expensive mistakes. A smart CNC machinist thinks through each operation and asks "what could go wrong here?" before hitting the start button.
The career side offers several paths depending on what interests you. Some machinists become CNC programming specialists and work on the really complex stuff that makes other people's heads hurt. Others focus on setup and can get any machine running smoothly.
The technology changes fast enough that you're always learning something new. Many successful machinists eventually open their own shops or move into management roles where they teach younger workers how to avoid the mistakes they made early on.
Educational Pathways for CNC Careers
CNC training starts with basic machining courses that teach you how metal cutting actually works. You can't jump straight into computer numerical control without knowing why cutting speeds matter or how different materials behave.
Most programs begin with manual machines - old-school mills and lathes where you turn handles by hand. This foundation helps you understand what's happening when the CNC machine does the same operations automatically.
Community colleges offer the best bang for your buck in CNC training. Programs typically run 6 months to 2 years and cover everything from blueprint reading to CNC programming.
Some schools have partnerships with local manufacturers who hire graduates directly. Technical institutes also run CNC programs, though they often cost more than community college options. Look for schools with modern CNC machines - learning on 20-year-old equipment won't prepare you for what shops actually use today.
Certification programs give you credentials that employers recognize. The National Institute for Metalworking Skills offers CNC machinist certificates that many shops respect.
Some manufacturers like Haas and Mazak run their own CNC training centers focused on their specific machines. These programs are shorter but more specialized.
Online CNC programming courses can supplement hands-on training, but you can't learn to run a CNC machine from watching videos alone.
Self-learning works for CNC programming if you already have machining experience. CAM software companies offer training materials for their programs.
YouTube has thousands of CNC videos, though quality varies wildly. Online forums where CNC machinists share tips and solve problems are goldmines of practical information.
But nothing replaces time spent next to actual CNC machines learning how computer numerical control systems behave in real production environments. The software side you can study at home, but machine operation requires hands-on practice.
CNC Programming Essentials
G-code sounds intimidating until you realize it's just a way to tell machines where to move. G01 means go in a straight line from here to there. G02 and G03 cut circles - one goes clockwise, the other goes the opposite way. Most CNC programming boils down to these basic moves repeated over and over. You're basically giving the machine a list of directions like "go to this spot, then that spot, then cut a curve."
M-code controls everything else the machine does besides moving around. M03 spins the cutting tool, M05 stops it. M06 tells the machine to grab a different tool from the tool changer.
You use M-code to turn coolant pumps on and off, open chuck jaws, or activate whatever other gadgets your particular machine has. Computer numerical control systems need both types of code working together.
Writing G-code by hand is like learning to write before using a word processor - it helps you understand what's really going on. Most shops use CAM software that writes the programs automatically.
You draw the part, pick your cutting tools, and the software spits out pages of G-code ready to run. But knowing how to read and edit that code saves time when you need to fix small problems.
The biggest CNC programming mistakes usually involve coordinates and tool changes. Set your work zero wrong and the machine cuts air instead of material. Forget to tell the spindle to start spinning and you just rub a dull tool against your workpiece.
Tool length measurements that are off by a few thousandths can crash tools or leave parts oversize. Smart programmers always simulate their programs on screen first, then run them slow the first time to catch problems before they turn expensive.
Economic Impact of CNC Machining
CNC machining changed how the world makes things, and the numbers prove it. Manufacturing used to require armies of skilled workers who took years to train properly.
Now one CNC machine can do the work of several manual machinists, and it never calls in sick or takes vacation days. Computer numerical control systems let small shops compete with big factories because precision doesn't depend on finding the perfect employee anymore.
The money side tells an interesting story. CNC machines cost serious cash upfront - a decent CNC machine runs six figures easy. But the payback comes from making parts faster and more consistently than manual methods.
A CNC machinist can set up a program and walk away while the machine runs for hours. Try doing that with manual equipment and see what happens to your scrap rate.
Production efficiency jumps dramatically when shops switch from manual to CNC technology. Parts that used to take days now get finished in hours.
Complex shapes that required multiple setups on different machines can often be completed in one CNC operation. Computer numerical control systems work around the clock too - many shops run lights-out production where CNC machines make parts all night without supervision.
The employment picture gets complicated though. CNC technology definitely eliminated some traditional machinist jobs, but it also created new opportunities.
CNC programming specialists earn good money, and someone still needs to set up and maintain all these machines. The difference is that modern manufacturing needs fewer people overall, but those people need more technical skills. Shops that invested in CNC machining early gained competitive advantages that manual operations simply cannot match.
The global manufacturing industry now depends on computer numerical control systems to meet quality and volume demands that manual methods never could achieve.
Comparative Analysis: CNC vs. Traditional Machining
Traditional machining puts everything in the operator's hands. You turn wheels to move cutting tools, watch dial indicators, and hope your measurements stay accurate.
Manual machines require skilled workers who learned their trade over years of practice. A good manual machinist can make amazing parts, but even the best ones have off days.
CNC machining removes most human variables from the equation by letting computer numerical control systems handle the precise movements.
Speed differences between the two methods are huge. Manual machining means stopping frequently to check dimensions and adjust settings.
CNC machines run continuously once programmed correctly. A manual machinist might make 10 parts per day while a CNC machine cranks out 100 of the same parts overnight. Computer numerical control systems also reduce setup time for repeat jobs - load the program and you're ready to go.
Quality consistency separates CNC technology from traditional methods more than anything else. Manual operators have good days and bad days, but CNC machines follow the same program exactly every time. Part number 1000 comes out identical to part number 1.
This repeatability is why manufacturing switched to computer numerical control - you get predictable results that meet specifications reliably.
Real shops show how dramatic the transition can be. A small automotive parts manufacturer switched their manual mills to CNC machines and doubled their output while cutting their scrap rate in half. They went from needing 5 skilled machinists to 2 CNC operators who could handle multiple machines.
Another shop making medical components found that CNC technology let them hold tolerances that were impossible with manual equipment. The computer numerical control systems paid for themselves within 18 months through reduced labor costs and eliminated rework. These aren't unusual stories - similar improvements happen wherever shops make the jump from traditional machining to CNC operations.
Future Trends in CNC Technology
CNC technology keeps getting smarter, and some of the new stuff feels like science fiction. Machines now monitor their own cutting tools and automatically replace them when they get dull. Computer numerical control systems can detect vibrations that signal trouble and adjust cutting speeds on the fly. Some CNC machines even learn from each part they make, getting better at avoiding problems over time.
Artificial intelligence is starting to show up in CNC machining in ways that actually make sense. Smart software watches how tools wear and predicts when they'll break before it happens.
This beats the old method of just hoping your cutting tools last until the job finishes. AI also helps with CNC programming by suggesting better tool paths and cutting speeds based on what worked well for similar parts in the past.
Automation around CNC machines is getting wild. Robot arms load parts and remove finished pieces while the CNC machine keeps cutting. Some factories run entire shifts with minimal human supervision - the computer numerical control systems talk to robots, automatic tool changers, and quality inspection equipment.
Workers focus on programming and troubleshooting while machines handle the repetitive stuff.
Environmental concerns are pushing CNC technology in new directions too. Newer machines use way less energy than older models, and some run completely on recycled cutting fluids. Manufacturers are designing CNC machines that last longer and need fewer replacement parts.
The precision of computer numerical control also reduces waste - you make parts right the first time instead of scrapping material due to human error. Some shops now use CNC machining specifically because it generates less waste than traditional manufacturing methods.
The trend points toward cleaner, more efficient production that still delivers the quality and speed that made CNC technology popular in the first place.